Coyote Ridge Environmental Assessment, US Green Building Council, 2009
Download original document:
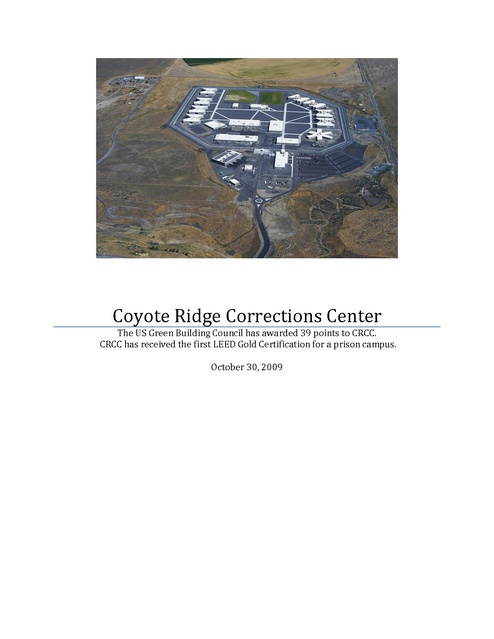
Document text
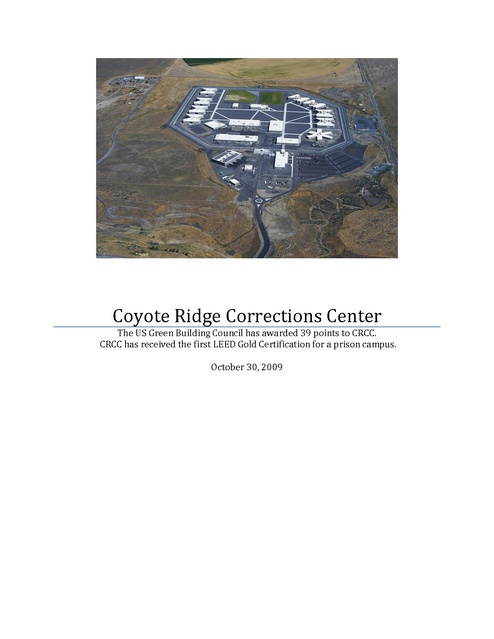
Document text
This text is machine-read, and may contain errors. Check the original document to verify accuracy.
Coyote Ridge Corrections Center The US Green Building Council has awarded 39 points to CRCC. CRCC has received the first LEED Gold Certification for a prison campus. October 30, 2009 OWNER INFORMATION Contact Name: David B. Jansen, P.E., LEED® AP Department of Corrections Director of Capital Programs 7345 Linderson Way SW, Tumwater, WA 98501 Phone: (360) 725-8354 Fax: (360) 586-8723 E-Mail: dbjansen@doc1.wa.gov PROJECT INFORMATION Coyote Ridge Corrections Center Expansion Connell, Washington Owner: State of Washington Department of Corrections/Department of General Administration Designer (A/E): Integrus Architecture (Contact Marcine Herron, 509-838-8681), Rosser International, MW Engineers, CH2MHill Constructor, Key Subcontractor or Vendors: Hunt/Lydig Joint Venture Construction Manager: Jack Olson, Project Director, General Administration Type of Contracts: General Administration Public Works contract for Design Build Project Summary: The $230 million dollar Coyote Ridge Corrections Center (CRCC) expansion is a new and innovative, state-of-the-art, 2,048 bed prison constructed for the State of Washington. Located in Connell, Washington, the project consisted of 578,400 square feet of inmate-housing and support space designed to minimize operating costs while maintaining security and maximizing the opportunity for rehabilitation of the incarcerated population. Between 2005 and 2008, this was the largest prison project in the United States and was also the largest non-Department of Transportation Public Works project in Washington State. The CRCC innovations in construction delivery, sustainability and housing methods are receiving national attention. Presentations were already provided to the annual meetings of the American Institute of Architects Academy of Architecture for Justice, and the Design Build Institute. The link below to the April 2009 Corrections Today and attached article illustrate the level of industry interest in this facility. http://viewer.zmags.com/showmag.php?mid=wpfdpq#/page34/ Cost Savings in Construction and Operation: The prison represents a new concept in incarceration designed to reduce both construction and operating costs. Viewed from the outside, CRCC is an intimidating and secure medium-security prison. However four of the housing units are based on an innovative “hybrid” concept that reduced construction costs and will reduce operating costs. The hybrid housing unit allows more internal freedom of movement to inmates who behave well in prison but cannot qualify for housing in lower cost minimumsecurity facilities because of their convictions. The hybrid buildings are finished on the inside with metal studs and sheetrock instead of steel and concrete as typically used in higher-security level facilities. This saved approximately $3 million per hybrid housing unit over the cost of a traditional medium housing unit. The simpler design uses less electronic technology, and requires less preventive maintenance than a traditional medium housing unit. These buildings also reduce the costs of operating the facility by requiring twelve fewer custody officers, providing an operational savings of more than $700,000 per year. The Department of Corrections recently received an energy rebate check for $118,000 for the energy efficient ventilation and boiler systems installed at CRCC. An additional rebate of over $300,000 is pending for the refrigeration and heat reclamation systems. Page 2 of 5 Construction Highlights: The project used the Design Build (DB) delivery method for construction. This decision enabled the owner to fast track the project and successfully reduced the project delivery time by a full year. The design and construction team worked with the owner to provide a seamless product that identified both cost and time savings for the project. The project also incorporated several large changes authorized by the legislature during the construction project; adding almost $30 million to the project without any additional contract time. Site preparation work included constructing an access road by filling a large gully with fill from site excavations, extending utilities to the site and adding water and wastewater capacity for the host community. The campus features eight twin-pod 256-bed housing units in a variety of configurations that can accommodate inmate classification levels from low- to medium-security plus a 100-bed administrative segregation unit. Support buildings include a medical facility, a state-of-the-art electronic control center that can see and control any part of the prison, a food preparation and serving area, a full-campus five megawatt backup power system, a visitor center, exercise and classroom facilities, an administrative office complex, and maintenance and warehouse facilities. CRCC also includes a Correctional Industries building that houses a food factory, laundry facilities and a sewing operation. The Correctional Industries services provide employment for inmates where they can learn job skills and earn a wage that helps pay for the cost of incarceration and victim’s compensation among other fees. An aerial photograph and key is provided for reference. Environmental and Leadership in Energy and Environmental Design (LEED) Features: Incorporating sustainability elements into a prison project presents a unique set of challenges during the design and construction process. Unlike the construction of a school, for example, the CRCC team had to balance opportunities for sustainability against the essential functions of safety and security at the correctional facility. The facility used 30 percent recycled content materials and only zero-to-low volatile organic carbon sealants and adhesives, paints and surface finishes, and carpeting and composite wood products. More than 30 percent of construction materials were manufactured in the region and 50 percent of wood products were sourced from Forest Stewardship Council-certified forests. Almost 95 percent of the construction waste was diverted from the landfill. Landscaping and irrigation are kept to a minimum to control water use in arid Eastern Washington. Natural light is used to reduce energy costs. In addition to the many energy and water conservation measures incorporated into the facility, CRCC also has solar panels on the Warehouse roof. The solar installation (added late in the project) incorporates flexible, lightweight rooftop photovoltaic panels that did not require the roofing structure to be reinforced. The photovoltaic panels offer reduced installation costs and comparable levels of efficiency and life cycle to the heavier, rigid conventional crystalline solar arrays and should also extend the life of the roof itself by providing an additional sealed layer. The project has applied for and received a unique, campus-wide Leadership in Energy and Environmental Design (LEED) certification. Although the CRCC project includes 21 individual buildings, the project submitted a single LEED certification submission for the entire campus. The US Green Building Council has awarded 39 points which means that CRCC has the first LEED Gold Certification for a prison campus. Page 3 of 5 Teamwork: The key to the success of the CRCC project was the team that planned, designed and constructed the new prison. Innovation and cost savings were provided by every member of the team. The team commitment was exemplified when the contractors united to donate a Religious Activity Center (RAC) building for the future inmates. Law requires that religious buildings at prisons must be constructed by voluntary contributions. Integrus Architecture donated a complete architectural and structural design. MW Engineers donated a mechanical, plumbing, and electrical design. Lydig Construction donated labor for the concrete work. Apollo Sheet Metal donated plumbing rough in. Berg Electric donated electrical service. And Hunt/Lydig donated the exterior walls and roof of the building. In addition to the many religious denominations who donated to the RAC, the community supported a “buy a yard of concrete” campaign that generated more than $8,000 to buy the concrete that Connell Sand & Gravel provided at cost. The value of the labor and materials donated exceeds $250,000. Financial Summary: The final approximate capital value including the land is $230.2 million. Additional budget details provided below: The 2005 Legislature authorized $179 million for the first phase of the CRCC Expansion to complete 1,280 new beds. (Five housing units) The 2006 Legislature authorized $50 million to complete an additional 512 beds. (Two additional housing units) The 2007 Legislature authorized $13.2 million to complete the project. (One more housing unit) The original design/build contract was for $160 million. The final contract amount was $190 million with the scope changes. (Total of 8 housing units with associated support structures) The final total budget was $230.2 million. The final design/build contract with sales tax was $205,672,000 SCHEDULE PERFORMANCE Scheduled contract was awarded in June 2006 Substantial completion date was originally April 2008 During the DB team selection process two additional housing units were added to the scope and the substantial completion date was moved to October 2008. A 60 day extension was granted to do the final startup and testing of some of the added scope work. (The last housing unit and other improvements added by the 2007 legislature) Actual Construction Start Date was May 19, 2006 The first buildings were turned over to the owner in March 2008, seven months ahead of schedule. Substantial completion date for the entire campus was December 31, 2008. Page 4 of 5 SAFETY PERFORMANCE OSHA Incidence Rate: 4.54 Lost Work Day Cases: 2.27 Approx. Total Work Hours: 705,479 CRCC Expansion – Key Team Members Request for Proposal Consultants HOK, San Francisco Ambia, Olympia KMB, Olympia DEI, Spokane Hargis, Spokane Clevenger Associates Design/Builder Hunt/Lydig, Joint Venture Integrus Architecture, Spokane Rosser International, Atlanta MW Engineers, Spokane CH2MHill, Spokane Berg Electric, Portland Apollo Sheet Metal, Pasco PCI Others City of Connell Anderson-Perry Engineers, Walla Walla Franklin County PUD Avista Utilities Century Tel Owner’s Representatives Jack A Olson, PE, Project Director; Department of General Administration Larry Hueter, Project Manager Kevin Loresch, Clerk-of-the Works Sam Harris, Clerk-of-the Works Page 5 of 5