Osha Report on Unicor Prison Recycling 2008
Download original document:
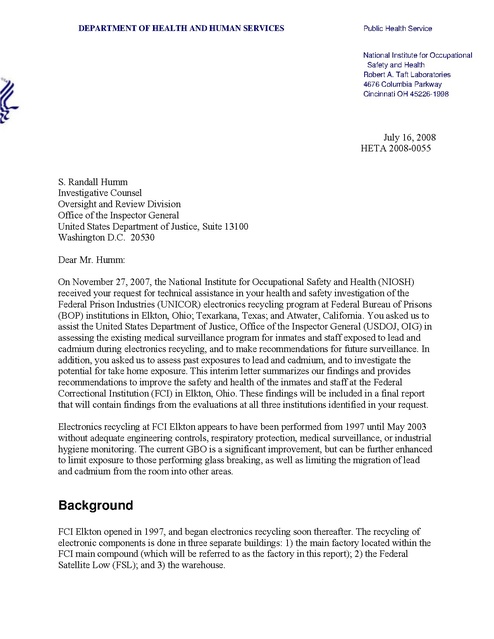
Document text
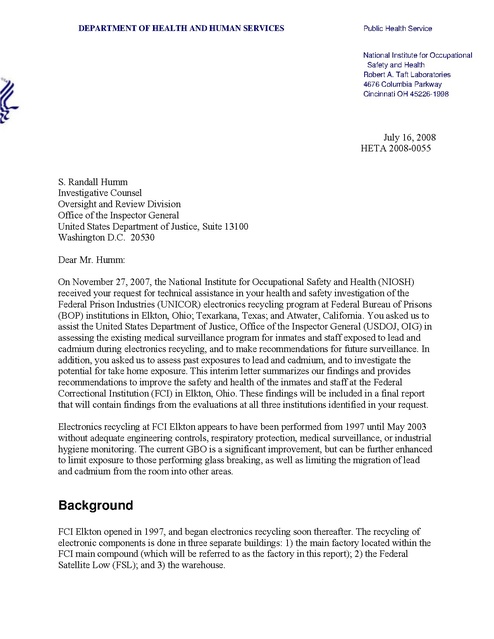
Document text
This text is machine-read, and may contain errors. Check the original document to verify accuracy.
DEPARTMENT OF HEALTH AND HUMAN SERVICES Public Health Service National Institute for Occupational Safety and Health Robert A. Taft Laboratories 4676 Columbia Parkway Cincinnati OH 45226-1998 July 16, 2008 HETA 2008-0055 S. Randall Humm Investigative Counsel Oversight and Review Division Office of the Inspector General United States Department of Justice, Suite 13100 Washington D.C. 20530 Dear Mr. Humm: On November 27, 2007, the National Institute for Occupational Safety and Health (NIOSH) received your request for technical assistance in your health and safety investigation of the Federal Prison Industries (UNICOR) electronics recycling program at Federal Bureau of Prisons (BOP) institutions in Elkton, Ohio; Texarkana, Texas; and Atwater, California. You asked us to assist the United States Department of Justice, Office of the Inspector General (USDOJ, OIG) in assessing the existing medical surveillance program for inmates and staff exposed to lead and cadmium during electronics recycling, and to make recommendations for future surveillance. In addition, you asked us to assess past exposures to lead and cadmium, and to investigate the potential for take home exposure. This interim letter summarizes our findings and provides recommendations to improve the safety and health of the inmates and staff at the Federal Correctional Institution (FCI) in Elkton, Ohio. These findings will be included in a final report that will contain findings from the evaluations at all three institutions identified in your request. Electronics recycling at FCI Elkton appears to have been performed from 1997 until May 2003 without adequate engineering controls, respiratory protection, medical surveillance, or industrial hygiene monitoring. The current GBO is a significant improvement, but can be further enhanced to limit exposure to those performing glass breaking, as well as limiting the migration of lead and cadmium from the room into other areas. Background FCI Elkton opened in 1997, and began electronics recycling soon thereafter. The recycling of electronic components is done in three separate buildings: 1) the main factory located within the FCI main compound (which will be referred to as the factory in this report); 2) the Federal Satellite Low (FSL); and 3) the warehouse. Page 2 – S. Randall Humm The glass breaking operation (GBO) is where cathode ray tubes (CRTs) from computer monitors or televisions are processed. Disassembly and glass breaking occurred at the factory from 1997 until early 2003 and the warehouse until about 2003, although staff at Elkton were unsure when glass breaking ended at the warehouse. Based upon our review of documents and interviews with staff and inmates conducted by DOJ and by us, it appears that there was no respiratory protection used or any type of engineering control in place to minimize exposures during the GBO until about 2001. At this time a “sawdust collection system” was installed at the factory, but not in the warehouse. It was also reported that some inmates began to use respiratory protection at this time. The type of respiratory protection is unknown. In April of 2003, construction of a glass breaking room was completed in the factory. The glass breaking room is divided into four areas by vinyl strip curtains hanging from the ceiling: an entry area, the GBO workstations, the ventilation discharge area, and the “clean area” where inmates don and doff coveralls and other personal protective equipment (PPE). There is a walk-off mat immediately outside the entrance to the room to reduce dust carryout on shoes. A local exhaust ventilation (LEV) system adapted from a spray painting operation is installed in the room. Two inmate glass breakers, who stand facing each other at the ends of a rectangular grated work surface (table), are oriented at 90 degrees to the LEV airflow entering the prefilter. Each workstation has two small rectangular hoods and fans mounted behind and just below the work surface that are intended to capture airborne dust above the Gaylord boxes containing broken CRT glass. The fans/hoods are not ducted, but discharge into the work area approximately 2 ½ to 3 feet from the face of the retrofitted spray painting LEV system. The discharge is directed toward the face of the LEV system. An inmate receives large open-top wooden and cardboard boxes with CRTs for the GBO, and stages the boxes outside the glass breaking room. Periodically, he uses a manual pallet jack to roll the boxes through the strip curtain into the area where the operation actually occurs, and to remove Gaylord boxes of broken glass from the room. Inmates who perform the GBO (“glass breakers”) enter the clean area where they don cloth coveralls, gloves, and a hooded powered air purifying respirator (PAPR), and then enter the glass breaking area. CRTs are placed on the grate where they are manually shattered with hammers. The glass breakers reach through a strip curtain at opposite ends of the grate to break funnel glass at one work station, and panel glass at the other. Broken glass falls into Gaylord boxes positioned below the grate. When inmates finish breaking glass, they return to the clean area in their coveralls and PAPR, use a high-efficiency particulate air (HEPA) filtered vacuum on their coveralls before removing them, then remove their PPE and leave the area. Staff enter the room only when there is no glass breaking going on to put away tools and search the area, otherwise they observe the inmates in the glass breaking room through the window or vinyl curtains. While housekeeping is a routine component of all production processes, a weekly extensive cleaning is conducted in the glass breaking area. During that operation no production takes place and all workers in this area remove settled dust by vacuuming and wet mopping. All surfaces, including walls, equipment, and floors are cleaned. The blanket pre-filter on the LEV system is vacuumed using the HEPA vacuum cleaner. Page 3 – S. Randall Humm Additionally, at approximately monthly intervals, the filters in the LEV system are removed and either cleaned or replaced. Prior to an evaluation by Federal Occupational Health (FOH) and the NIOSH Division of Applied Research Technology (DART) in March 2007, filters were removed and cleaned by vacuuming, shaking, or banging on the floor to shake dust out. This took most of the work shift and reportedly created a thick cloud of dust within the enclosed glass breaking room. This process was changed after the FOH-NIOSH/DART evaluation, and is reported to now be a wet process where the filters are wetted, removed, and bagged for disposal and new filters used as replacements. A chip recovery program began at the FSL in October 2005, and ended in October 2006. Computer chips were removed from the mother board by holding the mother board over either a lead solder pot or a lead solder wave fountain. Although the solder temperature was supposed to be maintained just above the melting point (reportedly 400 to 600 degrees F), staff reported that the solder temperature was set subjectively (i.e., the temperature was not measured), which may have resulted in overheating, producing lead fume. There was no LEV for the first several months of this operation until what was described by staff as a “make-shift PVC system” was installed. This LEV system was replaced the following year with a LEV system designed by a consultant. Despite the use of LEV at chip recovery stations, staff described a visible haze in the FSL, and expressed concern about exposure to lead fume from this operation. Assessment In response to your request we reviewed the following documents: · Results of medical surveillance provided by your office; · Results of biologic monitoring provided by the medical clinic at FCI Elkton; · Work instructions for the GBO and maintenance; · Rosters for inmates working in recycling that provided location and dates of work, provided by the factory manager; · Timelines for recycling operations provided by the American Federation of Government Employees (AFGE) Local 607; · DOJ interviews with staff and inmates; · Industrial hygiene sampling performed by consultants to UNICOR; · Findings and recommendations of industrial hygiene assessments performed by FOH; and · Draft report of the industrial hygiene assessment performed by the NIOSH/DART We conducted a site visit on February 21-22, 2008 with you and a representative of FOH . During this site visit we held an opening conference with FCI and UNICOR management, AFGE representatives, UNICOR recycling staff, and the health service administrators and regional medical director. After the conference we toured the FCI, including the recycling factory, the warehouse, and the FSL. We conducted informational meetings for FCI and UNICOR staff, and inmates. We spoke to several UNICOR staff who approached us after the meetings about their medical issues and how they might relate to exposures at the FCI. We also met with the safety manager, factory manager, and health services administrator. We ended the site visit with a closing conference where we presented our initial impressions and recommendations. Page 4 – S. Randall Humm We were told that BOP has had an industrial hygienist on staff for several years, and that UNICOR recently hired one. Neither of these individuals was present during our visit, and it is unclear what, if any role, they may have had in setting up or monitoring the electronic recycling program. On March 25, 2008, we conducted an industrial hygiene survey to determine if lead- and cadmium-bearing dust had migrated from the glass breaking room to other FCI buildings and work areas and if there was evidence of “take-home” contamination in inmate housing and privately-owned staff vehicles. The purpose of this survey was to gather additional information to complement the extensive body of industrial hygiene data collected by FOH and NIOSH/DART. The survey was preceded by a brief opening meeting with FCI and UNICOR management, AFGE representatives, and UNICOR recycling staff to explain the purpose of the site visit. Following the meeting, we were escorted to the factory and automated data processing (ADP), where we set up area air sampling pumps to assess airborne concentrations of lead, cadmium, and other elements (minerals and metals). Air samples were collected, digested, and analyzed according to NIOSH Method 7303 [NIOSH 2003a] with modifications for digestion. Wipe samples were collected from undisturbed dusty surfaces in ADP, as well as at air diffusers in ADP, inside air handling units serving the laundry, visiting room, education, chapel, ADP offices, and from the floor mat at the entrance to the glass breaking room. Wipe samples were collected from the floor in three inmate cubicles where inmates place their boots, and from combination locks on lockers in the cubicles. Wipe samples were collected from personal vehicles used by UNICOR staff. Flat surfaces (e.g., ADP work stations) were sampled by wiping a 100 square centimeter (cm2) area (10 cm2 x 10 cm2) according to the sampling procedure outlined in NIOSH Method 9102 [NIOSH 2003b]. Surface area was not considered when collecting wipe samples from non-flat surfaces such as padlocks and vehicle steering wheels. Hand wipe samples were collected according to the dermal sampling procedure outlined in NIOSH Method 9105 [NIOSH 2003c] Hand wipe samples were collected after workers had washed their hands at the end of the workday. All wipe samples were collected using Ghost Wipes, which were digested and analyzed for elements according to NIOSH Method 9102 [NIOSH 2003b] with modifications for digestion. Bulk samples of material were collected from beneath the stone roof ballast on the factory roof at the exhaust fan of the sawdust collection system that was in use from 2001 until May 2003. Bulk samples were digested and analyzed for elements according to NIOSH Method 7303 [NIOSH 2003a] with modifications for digestion. Page 5 – S. Randall Humm Results and Discussion 1 Medical surveillance Inmates Medical surveillance began in March 2003, immediately prior to the installation of the glass breaking room, for inmates in glass breaking and disassembly, and staff. It is performed annually and consists of limited biological monitoring but no physical examinations. Biological monitoring consists of blood lead levels (BLL), blood cadmium (CdB), urine cadmium (CdU), and urine beta-2-microglobulin (B-2-M), although not all inmates involved in GBO and disassembly received all of these tests. In addition, some inmates had urine lead, blood or urine arsenic or mercury, and serum B-2-M, none of which seem to have been based upon work exposures or indicated by work history. Paper copies of test results are maintained in both the inmate’s personal medical record and with UNICOR management; however, the factory manager has been unable to locate any medical surveillance results at this time. Each inmate’s medical records are transferred with them; no medical records are retained at Elkton after an inmate is either transferred or released. Inmates are only informed of the results of their biological monitoring if the results are abnormal. Although start dates were not available to us for all inmates working in the GBO, it does not appear that any inmate had biological monitoring performed preplacement. Because smoking can increase cadmium and lead burdens in the body, it is important to note that smoking has been banned throughout the FCI for inmates since 2004, although staff may smoke in designated areas. The results of the available inmate biological monitoring are summarized below by area. Because measurements on individual inmates and staff were sporadic and the number tested small, no group analyses were performed. Glass Breaking Operation We received biological monitoring results for 26 inmates who performed glass breaking. Each inmate was tested 1 to 5 times, for a total of 54 rounds of testing. Table 1 shows inmate BLLs by year collected. The laboratory’s limit of detection (LOD) for blood lead was 1.0 microgram per deciliter of whole blood (µg/dL). In general, BLLs declined over time. Five of the seven tests done in early 2003 were done in March or April and may reflect exposures to lead prior to installation of the glass breaking room, but do not reflect exposures prior to the installation of the sawdust ventilation system in 2001 because the half-life of lead in blood is too short. There were 50 CdB tests done on inmates from 2003-2007. The laboratory’s LOD for CdB was 0.5 microgram per liter (µg/L). Twenty-seven were below the LOD; the remainder ranged from 0.5-1.2 µg/L. The earliest CdB were done in June 2003. Six inmates were tested in June 2003, and three were below the LOD; the remainder ranged from 0.5-1.1 µg/L. These six CdB may 1 See Occupational exposure limits and health effects in Appendix . Page 6 – S. Randall Humm reflect exposures to cadmium prior to installation of the glass breaking room, but do not reflect exposures prior to the installation of the sawdust ventilation system in 2001 because the half-life of cadmium in blood is too short. There were 28 CdU measurements. More than one laboratory was used for this analysis. At the lab most commonly used the LOD was 1 µg/L and 23 measurements were below this LOD. Other labs had lower LODs. If the CdU was above the LOD, then it was adjusted to the urinary concentration of creatinine to control for the variability in urine dilution. The five that were above the LOD ranged from 0.5 micrograms per gram of creatinine (µg/g/Cr) to 1 µg/g/Cr. These CdU measurements do integrate exposure over time because the half-life of cadmium in the urine is years to decades. However, only one of these inmates worked in GBO prior to May 2001; his CdU was less than 1 µg/L. Six inmates had urinary B-2-M measured; these ranged from less than 10 to 54 µg/g/Cr. Glass Breaking Room Maintenance One inmate who performed cleaning and filter change-outs in the GBO was monitored for lead and cadmium exposure from April 2003 until 2007, prior to the change in the filter change-out process. His annual BLLs ranged from 10-4 µg/dL, with a progressive decline over time. His CdBs ranged from 0.5 to 0.8 µg/L, and his CdUs were less than the LOD of 1 µg/L. Another inmate who performs maintenance in the room was monitored in 2007 and 2008. His BLL was 5 in 2007, and was not done in 2008. CdB was 0.6 µg/L in 2007, and less than the LOD of 0.5 µg/L in 2008. CdUs were less than 1 µg/L. Chip Recovery We reviewed biological monitoring for 14 inmates who worked in the chip recovery area; all were tested on February 16, 2007, 4 months after the operation ceased. BLLs ranged from 1-5 µg/dL. CdB was below the LOD for four inmates, and the remainder ranged from 0.5-1.1 µg/dL. All but one CdU were below the LOD, and the remaining one was 0.6 µg/g/Cr. No inmates had urine B-2-M measured. Factory (not GBO) We reviewed the results of biological monitoring done in April 2007 for 14 inmates who worked in the factory, but did not perform glass breaking. Two had BLLs less than the LOD, and the others ranged from 1-3 µg/dL. A BLL of 8 µg/dL was found in one inmate monitored in 2003. Seven had CdBs below the LOD, and the remainder ranged from 0.5-1.0 µg/L. Twelve had CdU below the LOD of 1 µg/L, and the other two were 0.2 and 0.6 µg/g/Cr. None had urine B-2-M performed. Page 7 – S. Randall Humm Warehouse Fourteen inmates who worked in the warehouse, but did not perform glass breaking, had biological monitoring done in February 2007, almost 4 years after the GBO ceased in the warehouse. BLLs ranged from1-5 µg/dL. Seven had CdBs below the LOD, and the remainder ranged from 0.5-0.8 µg/L. All 14 had CdU below the LOD, and none had urine B-2-M performed. Clerks We reviewed biological monitoring results for 2 clerks, one from the factory and one from the FSL. One had testing annually from 2003-2005, the other was tested in 2007. There were three BLLs ranging from 1-2 µg/dL. Three of four CdBs were less than the LOD of 0.5 µg/L, and one was 0.6 µg/L. Two CdUs were less than the LOD of 1 µg/L, and one B-2-M was 40 µg/g/Cr. Results of other tests We reviewed biological testing results for which we were unable to determine the reason the testing was done on inmates. Two inmates had serum B-2-M above normal. This test is often used to determine prognosis in hematologic malignancies and for dialysis patients. It is difficult to interpret in this setting because no medical history is available. In addition, three inmates had elevated urinary total arsenic, and one also had an elevated blood arsenic. The arsenic results were speciated and found to be organic arsenic, the type of arsenic which is found in seafood and is not considered toxic. All other tests (urine lead, blood or urine arsenic and mercury) were within normal limits. UNICOR Staff UNICOR staff see their private physicians for medical surveillance so their exams are not standardized. We reviewed available medical records and found that most staff members had records for CdB, CdU, urine B-2-M, and zinc protoporphyrin (ZPP). Some had physical exams documented, some had urinalysis, complete blood count, pulmonary function tests, or chest xrays. We reviewed the biological monitoring and medical exams provided for 10 UNICOR staff, including nine of 11 recycling technicians who had worked in electronics recycling. Each was tested between 1 and 5 times between 2003 and 2007. Their testing was done by a number of different laboratories, and thus, the LOD and range of normal for the tests varied. For example the LOD for BLL was either 1 or 3 µg/dL. Eighteen BLLs were below the LOD, and seven ranged from 1-2.5 µg/dL. One employee had a BLL of 10 µg/dL, however his BLLs the year before and after were below the LOD. His urine B-2-M was elevated at 445 µg/g/Cr, but he had normal B-2-M levels the year before and after this test result. Standard medical practice usually dictates that a physician repeat a lone elevated test result to determine whether the result is spurious (such as from lab error) or actually elevated. The tests were not repeated at the time, so laboratory error cannot be ruled out. Twenty-five CdB were done; 12 were below an LOD of 0.5 Page 8 – S. Randall Humm µg/L, 2 were reported as zero, and the remainder ranged from 0.2-2.1 µg/L. Twenty-one CdU were done; 13 were below the LOD of 1 µg/L and the rest ranged from 0.1-0.7 µg/L. Eighteen urine B-2-M were done between 2003 and 2007, and all were normal with the exception noted above. Twenty-two ZPPs were done between 2003 and 2007, and all were normal. Interviews with Staff Five staff asked to speak with us after NIOSH’s public meeting with concerned Elkton staff on February 21, two of the five worked in recycling. One of the recycling staff reported having been diagnosed with iron deficiency anemia in the past year. This condition is not related to recycling work or other occupational exposures at FCI Elkton. The other reported an increase in the blood zinc level over the past year, however, when we reviewed this employee’s biological monitoring results, we found that it was the ZPP that had risen, and that the levels were still well within normal limits. ZPP is not related to blood zinc. Of note, both staff noted these reported conditions in the recent past, well after construction of the glass breaking room. An employee from an adjacent area reported bipolar disorder, and one from another building reported transverse myelitis, neither of which can be related to this workplace. Finally, another employee from the adjacent area reported seeing a private physician and being tested for lead and cadmium, and that both were below the LOD. Industrial Hygiene Records Review The OIG provided consultant reports, industrial hygiene sampling results, and laboratory analysis results for 13 surveys conducted at FCI Elkton between summer 2001 and November 2007. Twelve surveys were conducted by consultants to UNICOR, and one was conducted by FOH in conjunction with a NIOSH/DART evaluation. Five reports contained sampling data indicating worker exposures to cadmium at levels exceeding the OSHA action level, and two reports documented exposures above the OSHA permissible exposure limit (PEL) for cadmium. One of the reports documented lead exposure above the PEL during a now-discontinued filter change procedure. No industrial hygiene reports, sampling data, or laboratory analysis reports were provided for the period from 1998 until August 2001. According to information provided by the OIG, it appears that there are no industrial hygiene reports for this period; thus, we have no information or data to help us assess the potential for early exposures to lead, cadmium, and possible other agents when glass breaking occurred in other locations without local exhaust ventilation. Assuming that we received reports for all industrial hygiene evaluations and/or laboratory analyses conducted from 2001 through 2007, we noted that only two evaluations were conducted prior to 2004. Two surveys were performed in 2004; no industrial hygiene evaluations were conducted in 2005, other than an OSHA inspection which resulted in a serious citation for exposure above the cadmium PEL and inadequate engineering/work practice controls. Page 9 – S. Randall Humm Our review of the consultant reports found that two consultants hired by UNICOR measured worker exposures exceeding the OSHA action level for cadmium, but did not discuss the findings or the implications of exceeding the action level. This omission occurred during one of two surveys conducted in 2004, and two of five surveys in 2006. The quality of the reports, i.e., observations, discussion, recommendations, was greatly improved in 2007 when the most recent consultant and FOH independently evaluated the glass breaking process, ventilation, and work practices. 2001 A laboratory report of sample analysis, dated August 20, 2001, was provided to us. This analytical report contains no information regarding the type of sample (personal sample versus area sample), sample volume, location, the work being performed, PPE, or exposure control methods. Lead was measured in one of the two air samples that were analyzed for lead; cadmium was not detected. Wipe samples indicated quantifiable amounts of lead and cadmium on surfaces. June 2003 A laboratory report of sample analysis, dated June 3, 2003, was provided to us. Although this analytical report contains no information regarding sample type, work processes, PPE, or exposure control methods, the report does contain a record of sample volume along with results for cadmium and lead. Based on an average sample volume of 744 liters, and assuming that sampling was conducted at the usual rate of two liters per minute, the nine samples from late May 2003 provide an estimate of airborne concentrations throughout a 370 minute sampling period. The analytical results indicate that the airborne lead concentrations were likely below the OSHA action level; however, airborne cadmium concentrations may have exceeded the OSHA PEL in five of the nine samples, and may have exceeded the action level in one other sample (range: 3-37 micrograms per cubic meter of air [µg/m3]). It is important to note that, at best, these samples only provide an estimate of airborne concentrations at unknown sampling locations under unspecified conditions. If sampling flow rates were higher or lower than the typical rate of two liters per minute, the concentration estimates could be higher or lower than those noted here. 2004 Consultant reports were provided for two evaluations conducted during June 2004. On June 2, personal breathing zone (PBZ) samples were collected for three glass breakers and one feeder; four area samples were collected on June 2. All results were below the action level for lead and cadmium. Wipe samples determined the presence of lead and cadmium on surfaces in the work area. Sampling was repeated on June 18, and the consultant reported that samples collected on this date revealed “no overexposure;” however, results in the sample summary sheet show that a PBZ sample collected on one of three glass breakers indicated exposure to airborne cadmium at the OSHA PEL of 5 µg/m3. Although this sample did not prove statistical exceedance of the PEL, the report should have contained a recommendation for further evaluation, and guidance regarding OSHA requirements for periodic air and medical monitoring where workers are exposed above the action level. In addition, one of four area samples indicated an airborne cadmium concentration of 5 µg/m3. Wipe samples collected on June 18 indicated that surface contamination had been reduced in locations previously sampled on June 2. Wipe sampling was repeated on July 9; results were similar to those for the June 18 wipe samples. The consultant Page 10 – S. Randall Humm measured air velocity at three locations on June 18 to assess the direction and velocity of air into and through the GBO. The consultant’s report did not interpret these measurements with respect to the effectiveness of the LEV system. 2005 No consultant reports were provided for 2005. On September 8, 2005, OSHA conducted air monitoring for lead and cadmium that determined one of two glass breakers was exposed to cadmium above the PEL, and lead above the action level. UNICOR was cited for the overexposure and for inadequate engineering and work practice controls. 2006 A different environmental consulting firm was hired to conduct air sampling during glass breaking during site visits in January, February, June, July and September 2006. PBZ sampling results for two glass breakers and two workers outside the booth did not exceed the action level for cadmium or lead on January 17. Several air velocity measurements were obtained “to determine if sufficient general ventilation is provided within the glass breaking area.” No authoritative industrial hygiene references or guidelines were used to support the consultant’s conclusion that adequate ventilation was provided. Sampling and air velocity measurements were repeated on February 17. Air sampling results for this visit indicate that cadmium exposures exceeded the action level for one handler and one glass breaker. As in one of the 2004 consultant reports, this report did not note that the action level had been exceeded. The consultant returned on June 26 and 27 to conduct air sampling and assess ventilation in the GBO and chip recovery. Sample results indicate that a glass breaker was exposed to cadmium above the PEL, and a handler was exposed above the action level. As in earlier consultant reports, the report for June 26 did not mention or discuss the significance of exceeding the action level, nor did it provide guidance regarding medical surveillance, a written compliance program, and other OSHA requirements triggered when air sampling indicates worker exposure above the PEL. Air sampling conducted on June 27 at chip recovery in the FSL did not detect lead or cadmium above the analytical LODs. The consultant also collected air samples for ethylene glycol and n-propanol at chip recovery. It is not clear why these chemicals were selected for evaluation. The OIG provided two laboratory reports of sample analyses (both reports are dated July 10, 2006) which appear to be for wipe samples collected in GBO and chip recovery during the June evaluation. We did not find these laboratory results in the industrial hygiene reports that were provided to us. One report indicates small quantities of cadmium in five samples collected from surfaces in chip recovery (less than 4.8 µg/sample). The average quantity of lead in the five wipe samples was much greater: 1600 µg/sample (range 190 to 6800 µg/sample). Small quantities of cadmium and lead were measured in one sample collected from an inmate’s hands. The other laboratory report indicates that the average quantities of cadmium and lead in six surface wipe samples collected in the GBO was 35 µg/sample and 290 µg/sample respectively. The average amount of cadmium and lead in three hand wipe samples was 40 µg/sample for both elements. Page 11 – S. Randall Humm A consultant report for a July 7 survey indicates concentrations of cadmium and lead to be well below occupational exposure limits in five PBZ and five area air samples. A second report for this survey notes that cadmium and lead were measured in five surface wipe samples and three hand wipe samples. This report noted a need for more thorough cleaning of surfaces and hands. On September 6, the consultant collected five PBZ and five area samples. All results were below OELs. Hand wipe samples from three individuals (one staff, two inmates) measured 5.8, 340, and 870 µg-cadmium on their hands. The corresponding quantities of lead in the hand wipes was 26, 250, and 710 µg-lead/sample. The average quantity of cadmium and lead in five surface wipe samples was 240 µg (range 10 to 640 µg), and 19,000 µg (range 57 to 85,000 µg) respectively. 2007 On February 27 and 28, FOH collected air, wipe, bulk dust, and waste samples in the factory, warehouse, and FSL where electronics recycling had been conducted in the past, or was currently being conducted. Air sampling during two days of glass breaking indicated that worker exposures were below applicable occupational exposure limits (OELs). The report noted that the LEV system was adequately controlling exposure at the GBO during routine operations; however, air sampling during LEV filter change-out, a maintenance function, found airborne cadmium and lead concentrations well above the PELs. This overexposure, which exceeded the respirator protection factor, resulted from poor change-out procedures that included banging the dirty filters together to knock the dust off. The results of personal air monitoring in the warehouse and FSL were well below OELs. (Note: chip removal in the FSL had been discontinued in 2006.) Wipe samples in the factory, warehouse, and FSL found significant lead and cadmium contamination on various surfaces. This report concluded that the surface contamination does not pose an “imminent inhalation threat,” but could “be responded to in a prompt but well-coordinated manner.” FOH noted that migration of lead- and cadmium-bearing dust from the current GBO could be reduced by installing a three-stage decontamination room. On September 7, the third industrial hygiene consultant, for which we received reports, evaluated the GBO with PBZ sampling, surface wipe sampling, and assessment of the LEV system. Airborne cadmium was above the action level. Ventilation measurements and observations indicated apparent leakage in the LEV system. This report contained numerous recommendations regarding ventilation system repair, testing, and maintenance, as well as recommendations for improving work practices and use of PPE. On November 6, the industrial hygiene consultant conducted a subsequent evaluation of the GBO. Although all air sampling results were below the action levels for lead and cadmium, the results for one glass breaker indicated that his exposure approached the action level for cadmium. Wipe samples found various concentrations of lead and cadmium on surfaces in the glass breaking area. Page 12 – S. Randall Humm HHE Sampling, March 25, 2008 Wipe sample results are presented in Table 2. Wipe samples collected from three ceiling heating, ventilating and air-conditioning (HVAC) diffusers in ADP indicated concentrations of cadmium and lead ranging from 11-14 µg/100 cm2 and 49-55 µg/100 cm2 respectively. Lead and cadmium were found in a wipe sample of undisturbed dust on a ledge along the north wall of the ADP mezzanine, and in the mixed air plenum of air handler AH-3, which serves the factory tool room and ADP offices. These results indicate that undetermined concentrations of lead and cadmium migrated from the factory to ADP, possibly via the HVAC system. Given the low concentrations of airborne lead and cadmium determined by air sampling in 2007, it seems unlikely that significant migration of contaminants is occurring at this time. It is our opinion that the wipe sample results reflect much earlier workplace conditions, i.e., when glass breaking occurred in the middle of the factory with only a roof exhaust fan to remove airborne dust. Wipe samples, collected in three air handlers serving the laundry, education, visiting room, and chapel found quantifiable concentrations of lead and cadmium. Concentrations inside these air handlers were much lower than those inside AH-3 in the ADP. The route whereby these contaminants migrated to these air handlers is not clear. Two bulk samples of material beneath stone roof ballast on the factory roof at the exhaust fan of the sawdust collection system that was in use from 2001 until May 2003 contained 1000 and 1400 parts per million (ppm) lead (by weight), and 5000 and 7400 ppm cadmium (by weight). These samples provide evidence that glass breaking operations during the time the sawdust collection system was in use generated cadmium- and lead-bearing dust that was exhausted to the roof. Cadmium and lead contamination was found on the return air damper of rooftop air handler AHU-5HV1, which serves the factory. Given the low contaminant concentrations indicated by air sampling conducted by FOH and the current industrial hygiene consultant, we believe contamination inside this unit primarily reflects conditions prior to construction of the present glass breaking room. As shown in Table 2, quantifiable amounts of cadmium were present on the floor in three inmate cubicles where shoes are kept. Some lead was present in one cubicle. The presence of these metals on the floor indicates that some lead and cadmium is being tracked out of the glass breaking room. This finding is consistent with sample results showing lead on the soles of inmate and staff footwear (Table 2, samples W-27 and W-28). Hand wipe samples following hand washing by inmate workers demonstrated lead contamination on hands ranging from approximately 1.5 to 130 µg/wipe. This demonstrates that handwashing needs to be improved. Lead and cadmium contamination in two staff personal vehicles was generally below the limits of detection and/or quantitation; however, 3.3 µg-lead/100 cm2 was present on the center of the steering wheel in one vehicle. This indicates a potential for take-home contamination, but the concentration is minimal. Page 13 – S. Randall Humm Area air sampling results are shown in Table 3. One air sample indicated a quantifiable airborne concentration of lead and cadmium. This sample, which was collected within a few feet of the glass breaking operation (behind the strip curtain separating the GBO from the entry and changeout areas), was well-below applicable OELs. The area sample collected at the window in the GBO entry detected a trace concentration of lead and cadmium. The other six area air samples collected in the glass breaking room, factory, and ADP did not detect lead or cadmium. Conclusions Electronics recycling at FCI Elkton appears to have been performed from 1997 until May 2003 without adequate engineering controls, respiratory protection, medical surveillance, or industrial hygiene monitoring. Because of the lack of both biological monitoring and industrial hygiene data, we cannot determine the extent of exposure to lead and cadmium that occurred during that time frame, but descriptions of work tasks from staff and inmates indicate that exposures during that time frame were likely higher than current exposures. The current GBO is a significant improvement, but can be further enhanced to limit exposure to those performing glass breaking, as well as limiting the migration of lead and cadmium from the room into other areas. While some take-home contamination does occur, surface wipe sampling and biological monitoring suggest that take-home contamination does not pose a health threat at this time. Take-home contamination can be further reduced by changes to the GBO, work practices, and improved personal hygiene as recommended below. We cannot determine the extent of exposure to lead that occurred in the chip recovery process because of the lack of data. Descriptions of work tasks from staff, and a BLL of 5 µg/dL in an inmate 4 months after the process ended indicate that exposure to lead during this process did occur. We found no evidence that actions were taken to prevent exposure to lead at the outset in the chip recovery process and found that no medical surveillance was performed until after the process ended. Medical surveillance that has been carried out among inmates and staff has not complied with OSHA standards. No medical exams (including physical examinations) are done on inmates; staff receive inconsistent examinations and biological monitoring by their personal physicians; biological monitoring for lead is not done at established standard intervals; and results are not communicated to the inmates. Inappropriate biological monitoring tests have been done. Records of medical surveillance are not maintained by the employer for the appropriate length of time. At this time, after careful review of existing records and current operations, we conclude that the only persons with current potential for exposure to either lead or cadmium over the action level are the inmates who perform glass breaking or the monthly filter change-out. We believe that medical surveillance can be discontinued for all other inmates and staff. Some former inmates and/or staff may require surveillance under the OSHA cadmium standard. Wipe and bulk sample results indicated that lead- and cadmium-containing dust migrated out of the GBO in the past. Low levels of lead- and cadmium-containing dust on staff and inmate shoes and the floor mat outside the glass breaking room suggest that this is still occurring, although in small amounts. Contamination of inmate housing and staff vehicles is occurring, but is minimal; Page 14 – S. Randall Humm we have no data regarding the extent of past contamination in these locations. Hand washing is less than optimal for some individuals, including both staff and inmates. There is legacy contamination of the factory, FSL, and warehouse, which is scheduled to be remediated. We concur with FOH that surface contamination does not present an imminent hazard at this time, and should be remediated in a “prompt but well-coordinated manner.” Recommendations ` The following recommendations are provided to improve the safety and health of both the staff and inmates involved with electronics recycling at the Elkton FCI. 1. Continue to work with the current industrial hygiene consultant to increase the effectiveness of the LEV system. Improvements in the LEV system will not only reduce worker exposure to airborne contaminants, but will capture dust that would otherwise contribute to surface contamination, which could lead to an ingestion hazard (hand-to-mouth) or inhalation hazard if re-entrained. Conduct an industrial hygiene assessment to determine inmate exposure to lead and cadmium after the LEV is modified. 2. The change-out room should be reconfigured to ensure that GBO workers do not carry cadmium or lead out of the glass breaking room. Separate storage should be provided for nonwork uniforms and GBO work apparel/PPE. All potentially-contaminated work clothing and PPE should remain in the “dirty” chamber of the change-out room; non-work clothing should never come in contact with work items. As a minimum requirement, workers should be required to wash hands and all potentially exposed skin after doffing PPE, before putting on uniforms when exiting the GBO. Work clothes and PPE should never be worn outside of the GBO to minimize migration of cadmium- and lead-contaminated dust to other parts of the institution. Laundry personnel should be made aware of the potential exposure to lead and cadmium from work clothes and take action to minimize exposure to themselves. 3. Ensure full compliance with all applicable OSHA standards, including the General Industry Lead standard [29 CFR 1910.1025], the Cadmium Standard [29 CFR 1910.1027], the Hazard Communication Standard [29 CFR 1910.1200], and the Respiratory Protection Standard [29 CFR 1910.134]. This includes record keeping requirements, communication requirements, compliance plans, and medical surveillance. In addition to the OSHA requirements, we recommend that the preplacement examination for cadmium exposure be identical to the periodic examinations so that baseline health status may be obtained prior to exposure. 4. Contract a board-certified, residency-trained occupational medicine physician who is familiar with OSHA regulations on exposures at the FCI to oversee the medical surveillance program. BOP may be able to find a local physician, or contract with Federal Occupational Health. This contractor should also oversee medical clearance for respirators. 5. Carefully evaluate the qualifications and expertise of any consultant who may be hired to assess occupational or environmental health and safety issues. Anyone can present him/herself as an “industrial hygienist,” regardless of education, training, or expertise. One useful benchmark for vetting individuals who provide industrial hygiene services is the designation of Certified Page 15 – S. Randall Humm Industrial Hygienist (CIH). Certification by the American Board of Industrial Hygiene (ABIH) ensures that prospective consultants have met ABIH standards for education, ongoing training, and experience, and have passed a rigorous ABIH certification examination. The UNICOR and/or BOP industrial hygienists can assist in the selection of your consultants. 6. Perform a detailed job hazard analysis prior to beginning any new operation or before making changes to existing operations. This will allow BOP to identify potential hazards prior to exposing staff or inmates, and to identify appropriate controls and PPE. Involve the BOP and/or UNICOR industrial hygienists in these job hazard analyses. If medical surveillance is needed then BOP should perform pre-placement evaluations of exposed staff and inmates. 7. Appoint a union safety and health representative. This individual should be a regular participant on the joint labor-management safety committee that meets quarterly. Since inmates do not have a mechanism for representation on this committee, ensure that they are informed of its proceedings and that they have a way to voice their concerns about and ideas for improving workplace safety and health. This interim letter will be included in a final report that will include visits to two other BOP facilities. Please post a copy of this letter for 30 days at or near work areas of affected staff and inmates. Thank you for your cooperation with this evaluation. If you have any questions, please do not hesitate to contact us at 513-841-4382. Sincerely yours, Elena H. Page, M.D., M.P.H. Medical Officer David Sylvain, M.S., C.I.H. Industrial Hygienist Hazard Evaluations and Technical Assistance Branch Division of Surveillance, Hazard Evaluations and Field Studies cc: J. T. Shartle, Warden, FCI Elkton Bill Meek, Vice-President, AFGE Local 607 Paul Laird, Assistant Director, UNICOR Page 16 – S. Randall Humm Tables Table 1. Blood lead levels of inmates doing glass breaking, by year HETA 2008-0055, Federal Bureau of Prisons, FCI Elkton, Elkton, OH Mean BLL Median BLL Range Number (µg/dL) (µg/dL) (µg/dL) sampled 2003 5.6 4.5 3-9 7 2004 3.7 3.0 2-7 7 2005 3.7 3.9 2-10 12 2006 2.3 2.0 1-5 13 2007 1.7 1.5 1-4 10 Year HETA 2008-0055 Federal Bureau of Prisons FCI Elkton, Elkton, OH Table 2. Wipe sampling results, March 25, 2008 Sample ID Location Surface Approx. Elevation (feet) Description Area Wiped 2 W-1 HVAC diffuser ~15 W-2 desktop 2½ HVAC diffuser 15 W-4 desktop 2½ W-5 HVAC diffuser 15 W-6 desktop 2½ W-3 ADP row ADP4 above workstation C116 Workstation C116 near center of room; Row ADP4 above workstation C025 workstation C025 southwest corner of ADP; Row ADP1 above workstation C007 workstation C007 Cadmium Lead 2 2 cm µg/wipe µg/100 cm µg/wipe µg/100 cm 200 27 14 110 55 100 nd -- nd -- 200 21 11 97 49 100 trace -- nd -- 200 28 14 110 55 100 nd -- nd -- Page 17 – S. Randall Humm HETA 2008-0055 Federal Bureau of Prisons FCI Elkton, Elkton, OH Table 2. (Continued) Wipe sampling results, March 25, 2008 Sample ID Location Surface Approx. Elevation (feet) Description Area Wiped 2 W-7 C-beam 8 Factory Mezzanine mixed air plenum, AH-3 W-8 n/a ledge along north wall serves offices along north wall from factory tool room to ADP Lead 2 2 µg/wipe µg/100 cm µg/wipe µg/100 cm 100 820 820 970 970 315 70 22 430 140 100 53 53 55 55 not determined 1400 1200 32 ADP Mezzanine C-beam W-10 Factory Roof return air damper AHU-5HV1 n/a W-11 Mechanical Room laundry filter brace return air 5-AH2 n/a serves laundry not determined 4.9 W-12 Mechanical Room laundry Mixed air plenum 5-AH2 n/a serves laundry 315 2.1 0.67 19 6.0 W-13 Mechanical Room Outside air plenum 5-AH4 n/a serves education 270 8.3 3.1 46 17 W-14 Mechanical Room mixed air plenum 5-AH5 100 2.7 2.7 16 16 100 0.14 0.14 nd -- not determined 13 100 0.19 not determined 0.19 100 0.23 not determined 0.10 nd 28 130 7.2 41 0.23 trace W-9 W-15 C/D Unit D-A cube 51U W-16 W-17 C/D Unit D-A cube 29L floor, inmate cubicle combination lock on inmate locker floor, inmate cubicle W-18 combination lock on inmate locker W-19 floor, inmate cubicle C/D Unit D-B cube 005 8 n/a 0 ledge along north wall Cadmium cm serves visiting room and chapel where shoes are kept 1½ 0 where shoes are kept 1½ 0 where shoes are kept nd 0.19 nd nd 0.23 2.2 W-20 combination lock on inmate locker 1½ W-21 hands, inmate #1 n/a W-22 hands, inmate #2 n/a W-23 hands, inmate #3 n/a W-24 hands, inmate #4 n/a 0.51 4.3 W-25 hands, inmate #5 n/a 11 41 Factory hand wipe after washing hands at end of workday in glass breaking not determined -- 2.2 Page 18 – S. Randall Humm HETA 2008-0055 Federal Bureau of Prisons FCI Elkton, Elkton, OH Table 2. (Continued) Wipe sampling results, March 25, 2008 Sample ID Location Surface Approx. Elevation (feet) Description Area Wiped 2 cm W-25 hands, inmate #5 W-26 hands, inmate #6 W-27 sole of right shoe, staff W-28 Factory (continued) sole of sneaker, inmate #4 exterior, locker #2 W-29 µg/wipe 2 µg/100 cm 11 41 n/a not determined 2.2 3.1 n/a worn in glass breaking not determined 3.1 120 n/a sneaker not worn while working not determined 4.3 200 6 locker door in glass breaking decon area 100 trace -- nd 1½ glass breaking decon area 100 0.30 0.30 9.8 100 3.9 3.9 490 490 100 7.2 7.2 1000 1000 trace -- 3.3 3.3 n/a bench seat W-31 floor mat 0 W-32 floor mat 0 personal vehicle (Jeep) Lead 2 µg/100 cm hand wipe after washing hands at end of workday in glass breaking W-30 W-39 Cadmium µg/wipe entry to glass breaking room center of steering wheel 9.8 steering wheel n/a steering wheel n/a 100 not determined W-41 driver's seat n/a 100 trace -- nd -- W-42 console-arm rest n/a 0.14 0.14 trace -- steering wheel n/a 100 not determined 0.098 carpet n/a 100 nd W-40 W-43 W-44 personal vehicle (Mazda) left side at foot rest trace trace 2.3 -- trace -- Page 19 – S. Randall Humm Table 3. Area air sampling for lead and cadmium HETA 2008-0055, Federal Bureau of Prisons, FCI Elkton, Elkton, OH Location HEPA discharge area behind glass breaking At window in glass breaking Stanchion next to glass breaking Change-out area near clock Mezzanine rail above glass breaking At vinyl strip curtain in glass breaking entry ADP, east center ADP, west center NIOSH REL-TWA OSHA PEL-TWA ACGIH TLV Sampling Period (minutes) Sample Volume (liters) Cadmium Concentration 3 (µg/m ) Lead Concentration 3 (µg/m ) 407 810 nd nd 408 816 trace trace 376 753 0.31 4.6 406 808 nd nd 403 802 nd nd 387 380 381 774 760 762 nd nd nd Ca 5 10 nd nd nd 50 50 50 “nd” (not detected) indicates that the sample result is below the analytical limit of detection. The limits of detection for cadmium and lead are 0.02 ug/wipe and 0.6 ug/wipe, respectively. “trace” indicates that the sample result is between the analytical limits of detection and quantitation. The limits of quantitation for cadmium and lead are 0.077 ug/wipe and 1.9 ug/wipe, respectively. See the Appendix for a discussion of NIOSH recommended exposure limits (RELs), OSHA permissible exposure limits (PELs), and ACGIH Threshold Limit Values (TLVs). “Ca” indicates that NIOSH regards cadmium as a potential occupational carcinogen and that exposures should be reduced to the lowest feasible concentration. References NIOSH [2003a]. Elements by ICP: Method 7303. In: NIOSH Manual of Analytic Methods, 4th ed, 3rd Suppl. Cincinnati, OH: U.S. Department of Health and Human Services, Centers for Disease Control and Prevention, National Institute for Occupational Safety and Health, DHHS (NIOSH) Publication No. 03-127. NIOSH [2003b]. Elements on wipes: Method 9102. In: NIOSH Manual of Analytic Methods, 4th ed, 3rd Suppl. Cincinnati, OH: U.S. Department of Health and Human Services, Centers for Disease Control and Prevention, National Institute for Occupational Safety and Health, DHHS (NIOSH) Publication No. 03-127. NIOSH [2003c]. Lead in dust wipes by chemical spot test (colorimetric screening method): Method 9105. In: NIOSH Manual of Analytic Methods, 4th ed, 3rd Suppl. Cincinnati, OH: U.S. Department of Health and Human Services, Centers for Disease Control and Prevention, National Institute for Occupational Safety and Health, DHHS (NIOSH) Publication No. 03-127. Page 20 – S. Randall Humm Appendix Occupational exposure limits and health effects In evaluating the hazards posed by workplace exposures, NIOSH investigators use both mandatory (legally enforceable) and recommended occupational exposure limits (OELs) for chemical, physical, and biological agents as a guide for making recommendations. OELs have been developed by Federal agencies and safety and health organizations to prevent the occurrence of adverse health effects from workplace exposures. Generally, OELs suggest levels of exposure to which most workers may be exposed up to 10 hours per day, 40 hours per week for a working lifetime without experiencing adverse health effects. However, not all workers will be protected from adverse health effects even if their exposures are maintained below these levels. A small percentage may experience adverse health effects because of individual susceptibility, a pre-existing medical condition, and/or a hypersensitivity (allergy). In addition, some hazardous substances may act in combination with other workplace exposures, the general environment, or with medications or personal habits of the worker to produce health effects even if the occupational exposures are controlled at the level set by the exposure limit. Also, some substances can be absorbed by direct contact with the skin and mucous membranes in addition to being inhaled, which contributes to the individual’s overall exposure. Most OELs are expressed as a time-weighted average (TWA) exposure. A TWA refers to the average exposure during a normal 8- to 10-hour workday. Some chemical substances and physical agents have recommended short-term exposure limit (STEL) or ceiling values where health effects are caused by exposures over a short-period. Unless otherwise noted, the STEL is a 15-minute TWA exposure that should not be exceeded at any time during a workday, and the ceiling limit is an exposure that should not be exceeded at any time. In the U.S., OELs have been established by Federal agencies, professional organizations, state and local governments, and other entities. Some OELs are legally enforceable limits, while others are recommendations. The U.S. Department of Labor Occupational Safety and Health Administration’s (OSHA) permissible exposure limits (PELs) (29 CFR 2 1910 [general industry]; 29 CFR 1926 [construction industry]; and 29 CFR 1917 [maritime industry]) are legal limits enforceable in workplaces covered under the Occupational Safety and Health Act. NIOSH recommended exposure levels (RELs) are recommendations based on a critical review of the scientific and technical information available on a given hazard and the adequacy of methods to identify and control the hazard. NIOSH RELs can be found in the NIOSH Pocket Guide to Chemical Hazards [NIOSH 2005]. NIOSH also recommends different types of risk management practices (e.g., engineering controls, safe work practices, worker education/training, personal protective equipment, and exposure and medical monitoring) to minimize the risk of exposure and adverse health effects from these hazards. Other OELs that are commonly used and cited in the U.S. include the threshold limit values (TLVs) recommended by the American conference of Governmental Industrial Hygienists (ACGIH), a professional organization, and the Workplace 2 Code of Federal Regulations. See CFR in references. Page 21 – S. Randall Humm environmental exposure limits (WEELs) recommended by the American Industrial Hygiene Association, another professional organization. ACGIH TLVs are considered voluntary exposure guidelines for use by industrial hygienists and others trained in this discipline “to assist in the control of health hazards” [ACGIH 2007]. WEELs have been established for some chemicals “when no other legal or authoritative limits exist” [AIHA 2007]. Outside the U.S., OELs have been established by various agencies and organizations and include both legal and recommended limits. Since 2006, the Berufsgenossenschaftlichen Institut für Arbeitsschutz (German Institute for Occupational Safety and Health) has maintained a database of international OELs from European Union member states, Canada (Québec), Japan, Switzerland, and the U.S. [http://www.hvbg.de/e/bia/gestis/limit_values/index.html]. The database contains international limits for over 1250 hazardous substances and is updated annually. Employers should understand that not all hazardous chemicals have specific OSHA PELs, and for some agents the legally enforceable and recommended limits may not reflect current healthbased information. However, an employer is still required by OSHA to protect its employees from hazards even in the absence of a specific OSHA PEL. OSHA requires an employer to furnish employees a place of employment free from recognized hazards that cause or are likely to cause death or serious physical harm [Occupational Safety and Health Act of 1970 (Public Law 91–596, sec. 5(a)(1))]. Thus, NIOSH investigators encourage employers to make use of other OELs when making risk assessment and risk management decisions to best protect the health of their employees. NIOSH investigators also encourage the use of the traditional hierarchy of controls approach to eliminate or minimize identified workplace hazards. This includes, in order of preference, the use of: (1) substitution or elimination of the hazardous agent, (2) engineering controls (e.g., local exhaust ventilation, process enclosure, dilution ventilation), (3) administrative controls (e.g., limiting time of exposure, employee training, work practice changes, medical surveillance), and (4) personal protective equipment (e.g., respiratory protection, gloves, eye protection, hearing protection). Control banding, a qualitative risk assessment and risk management tool, is a complementary approach to protecting worker health that focuses resources on exposure controls by describing how a risk needs to be managed [http://www.cdc.gov/niosh/topics/ctrlbanding/]. This approach can be applied in situations where OELs have not been established or can be used to supplement the OELs, when available. Lead Occupational exposure to lead occurs via inhalation of lead-containing dust and fume and ingestion from contact with lead-contaminated surfaces. In cases where careful attention to hygiene (for example, handwashing) is not practiced, smoking cigarettes or eating may represent another source of exposure among workers who handle lead. Industrial settings associated with exposure to lead and lead compounds include smelting and refining, scrap metal recovery, automobile radiator repair, construction and demolition (including abrasive blasting), and firing range operations [ACGIH 2001]. Occupational exposures also occur among workers who apply and/or remove lead-based paint or among welders who burn or torch-cut metal structures. Page 22 – S. Randall Humm Acute lead poisoning, with blood lead levels (BLLs) usually over 70 micrograms per deciliter of whole blood (µg/dL), presents with abdominal pain, hemolytic anemia, neuropathy, and has in very rare cases progressed to encephalopathy and coma [Moline and Landrigan 2005]. Symptoms of chronic lead poisoning include headache, joint and muscle aches, weakness, fatigue, irritability, depression, constipation, anorexia, and abdominal discomfort [Moline and Landrigan 2005]. Overt symptoms usually do not develop until the BLL reaches 30-40 µg/dL [Moline and Landrigan 2005]. Overexposure to lead may also result in damage to the kidneys, anemia, high blood pressure, impotence, and infertility and reduced sex drive in both sexes. Studies have shown subclinical effects on heme synthesis, renal function, and cognition at BLLs <10 µg/dL [ATSDR 2007]. Inorganic lead is reasonably anticipated to cause cancer in humans [ATSDR 2007]. In most cases, an individual's BLL is a good indication of recent exposure to lead, with a half-life (the time interval it takes for the quantity in the body to be reduced by half its initial value) of 12 months [Lauwerys and Hoet 2001; Moline and Landrigan 2005; NCEH 2005;]. The majority of lead in the body is stored in the bones, with a half-life of years to decades. Bone lead can be measured using x-ray techniques, but these are primarily research based and are not widely available. Elevated zinc protoporphyrin (ZPP) levels have also been used as an indicator of chronic lead intoxication, however, other factors, such as iron deficiency, can cause an elevated ZPP level, so the BLL is a more specific test for evaluating occupational lead exposure. In 2000, NIOSH established an REL for inorganic lead of 50 micrograms per cubic meter of air (μg/m3) as an 8-hour TWA. This REL is consistent with the OSHA PEL, which is intended to maintain worker BLLs below 40 µg/dl; medical removal is required when an employee has a BLL of 60 µg/dL, or the average of the last 3 tests at 50 µg/dL or higher [29 CFR 1910.1025; 29 CFR 1962.62]. NIOSH has conducted a literature review of the health effects data on inorganic lead exposure and finds evidence that some of the adverse effects on the adult reproductive, cardiovascular, and hematologic systems, and on the development of children of exposed workers can occur at BLLs as low as 10 µg/dl [Sussell 1998]. At BLLs below 40 µg/dl, many of the health effects would not necessarily be evident by routine physical examinations but represent early stages in the development of lead toxicity. In recognition of this, voluntary standards and public health goals have established lower exposure limits to protect workers and their children. The ACGIH TLV for lead in air is 50 µg/m3 as an 8-hour TWA, with worker BLLs to be controlled to ≤ 30 µg/dl. A national health goal is to eliminate all occupational exposures that result in BLLs >25 µg/dl [DHHS 2000]. The Third National Report on Human Exposure to Environmental Chemicals (TNRHEEC) found the geometric mean blood lead among non-institutionalized, civilian males in 2001-2002 was 1.78 µg/dL [National Center for Environmental Health 2005]. OSHA requires medical surveillance on any employee who is or may be exposed to an airborne concentration of lead at or above the action level, which is 30 µg/m3 as an 8-hour TWA for more than 30 days per year [29 CFR 1910.1025]. Blood lead and ZPP levels must be done at least every 6 months, and more frequently for employees whose blood leads exceed certain levels. In Page 23 – S. Randall Humm addition, a medical examination must be done prior to assignment to the area, and should include detailed history, blood pressure measurement, blood lead, ZPP, hemoglobin and hematocrit, red cell indices, and peripheral smear, blood urea nitrogen (BUN), creatinine, and a urinalysis. Additional medical exams and biological monitoring depend upon the circumstances, for example, if the blood lead exceeds a certain level. Cadmium Cadmium is a metal that has many industrial uses, such as in batteries, pigments, plastic stabilizers, metal coatings, and television phosphors [ACGIH 2001]. Workers may inhale cadmium dust when sanding, grinding, or scraping cadmium-metal alloys or cadmiumcontaining paints [ACGIH 2001]. Exposure to cadmium fume may occur when materials containing cadmium are heated to high temperatures, such as during welding and torching operations; cadmium-containing solder and welding rods are also sources of cadmium fume. In addition to inhalation, cadmium may be absorbed via ingestion; non-occupational sources of cadmium exposure include cigarette smoke and dietary intake [ACGIH 2001]. Early symptoms of cadmium exposure may include mild irritation of the upper respiratory tract, a sensation of constriction of the throat, a metallic taste and/or cough. Short-term exposure effects of cadmium inhalation include cough, chest pain, sweating, chills, shortness of breath, and weakness [Thun et al. 1991]. Short-term exposure effects of ingestion may include nausea, vomiting, diarrhea, and abdominal cramps [Thun et al. 1991]. Long-term exposure effects of cadmium may include loss of the sense of smell, ulceration of the nose, emphysema, kidney damage, mild anemia, and an increased risk of cancer of the lung, and possibly of the prostate [ATSDR 1999]. The OSHA PEL (29 CFR 1910.1027) for cadmium is 5 μg/m3 TWA [CFR 1993]. The ACGIH has a TLV for total cadmium of 10 μg/m3 (8-hour TWA), with worker cadmium blood level to be controlled at or below 5 μg/dL and urine level to be below 5 μg/g creatinine, and designation of cadmium as a suspected animal carcinogen [ACGIH 2007]. NIOSH recommends that cadmium be treated as a potential occupational carcinogen and that exposures be reduced to the lowest feasible concentration [NIOSH 1984]. Blood cadmium levels measured while exposure is ongoing reflect fairly recent exposure (in the past few months). The half-life is biphasic, with rapid elimination (half-life approximately 100 days) in the first phase, but much slower elimination in the second phase (half-life of several years) [Lauwerys and Hoet 2001; Franzblau 2005]. Urinary cadmium levels are reflective of body burden and have a very long half-life of 10-20 years [Lauwerys and Hoet 2001]. OSHA requires medical surveillance on any employee who is or may be exposed to an airborne concentration of cadmium at or above the action level, which is 2.5 µg/m3 as an 8-hour TWA for more than 30 days per year [29 CFR 1910.1027]. A preplacement examination must be provided, and shall include a detailed history, and biological monitoring for urine cadmium (CdU) and beta-2-microglobulin (B-2-M), both standardized to grams of creatinine (g/Cr), and blood cadmium (CdB), standardized to liters of whole blood (lwb). OSHA defines acceptable CdB levels as < 5 µg/L, CdU as < 3 µg/g/Cr, and B-2-M as < 300 µg/g/Cr. NHANES III found geometric mean CdB of 0.4 µg/L among men in 1999-2000. The geometric mean CdU for men in 2001-2002 was 0.2 µg/g/Cr. Smokers can have CdB levels double that of nonsmokers Page 24 – S. Randall Humm [Lauwerys and Hoet 2001]. Periodic surveillance is also required one year after the initial exam and at least biennially after that. Periodic surveillance shall include the biological monitoring, history and physical examination, a chest x-ray (frequency to be determined by the physician after the initial x-ray), pulmonary function tests, blood tests for BUN, complete blood count (CBC), and Cr, and a urinalysis. Men over 40 years of age require a prostate examination as well. The frequency of periodic surveillance is determined by the results of biological monitoring and medical examinations. Biological monitoring is required annually, either as part of the periodic surveillance or on its own. We recommend that the preplacement examination be identical to the periodic examinations so that baseline health status may be obtained prior to exposure. Termination of employment examinations, identical to the periodic examinations, are also required. The employer is required to provide the employee with a copy of the physician’s written opinion from these exams and a copy of biological monitoring results within 2 weeks of receipt. Biological monitoring is also required for all employees who may have been exposed at or above the action level unless the employer can demonstrate that the exposure totaled less than 60 months. In this case it must also be conducted one year after the initial testing. The need for further monitoring for previously exposed employees is then determined by the results of the biological monitoring. Zinc Zinc is a very common element in the earth’s crust, and is found in air, soil, water, and foods. It has many industrial uses. For example, metallic zinc is used to galvanize other metals, and zinc compounds are used in paints, ceramics, rubber products, and in many drug products, like ointments, sunscreen, vitamins, and shampoos. Zinc is an essential element, which means it is required for the body to function properly. Zinc is not well absorbed through the skin, but is absorbed through the gastrointestinal system. Inhalational exposure to high levels of zinc oxide fume (generally above 75 mg/m3) can cause metal fume fever. [ATSDR 2005]. Metal fume fever is a syndrome of cough, shortness of breath, fever, aches, chills, and a high white blood cell count that occurs within hours of exposure, and can last up to 4 days. Normal serum or plasma zinc levels are about 1 mg/mL [ATSDR 2005]. The OSHA PEL and the NIOSH REL for zinc oxide are 5 mg/m3. This is 100 times higher than the PEL for lead, and reflects the relatively low toxicity of zinc. There is no mandated medical surveillance for workers exposed to zinc. References ACGIH [2001]. 2001 Documentation of the threshold limit values and biological exposure indices. Cincinnati, OH: American Conference of Governmental Industrial Hygienists. ACGIH [2007]. 2007 TLVs® and BEIs®: threshold limit values for chemical substances and physical agents and biological exposure indices. Cincinnati, OH: American Conference of Governmental Industrial Hygienists. Page 25 – S. Randall Humm AIHA [2007]. 2007 Emergency response planning guidelines (ERPG) & workplace environmental exposure levels (WEEL) handbook. Fairfax, VA: American Industrial Hygiene Association. ATSDR [1999]. Toxicological profile for Cadmium. Atlanta, GA: U.S. Department of Health and Human Services, Public Health Service. ATSDR [2005]. Toxicological profile for Zinc. Atlanta, GA: U.S. Department of Health and Human Services, Public Health Service. ATSDR [2007]. Toxicological profile for Lead. Atlanta, GA: U.S. Department of Health and Human Services, Public Health Service. CFR. Code of Federal Regulations. Washington, DC: U.S. Government Printing Office, Office of the Federal Register. CFR [29 CFR 1910.1027 (1993)]. Code of Federal Regulations. Washington, DC: U.S. Government Printing Office, Office of the Federal Register. CFR. OSHA lead standard for general industry. 29 CFR, Part 1910.1025. Washington, DC: U.S. Government Printing Office, Office of the Federal Register. CFR. OSHA construction industry lead standard. 29 CFR, Part 29 CFR 1926.62. Washington, DC: U.S. Government Printing Office, Office of the Federal Register. DHHS [2000]. Healthy people 2010: Understanding and Improving Health. 2nd ed. Washington, DC: U.S. Department of Health and Human Services. Available on the internet at: www.health.gov/healthypeople/Document/default.htm Franzblau A [2005]. Cadmium. Chapter 39.4. In: Textbook of clinical occupational and environmental medicine, Rosenstock L, Cullen MR, Brodkin CA, and Redlich CA, eds., 2nd ed. Philadelphia, PA: Elsevier Saunders, pp. 955-958. Lange JH, [2001]. A Suggested Lead Surface Concentration Standard for Final Clearance of Floors in Commercial and Industrial Buildings; Indoor Built Environment 10:48-51. Lauwerys RR, Hoet P [2001]. Chapter 2. Biological monitoring of exposure to inorganic and organometallic substances. In: Industrial chemical exposure: guidelines for biological monitoring. 3rd ed. Boca Raton, FL: CRC Press, LLC, pp. 21-180. Moline JM, Landrigan PJ. [2005]. Lead. Chapter 39.8. In: Textbook of clinical occupational and environmental medicine, Rosenstock L, Cullen MR, Brodkin CA, and Redlich CA, eds., 2nd ed. Philadelphia, PA: Elsevier Saunders, pp. 967-979. NCEH [2005]. Third national report on human exposure to environmental chemicals. Atlanta, GA: U.S. Department of Health and Human Services, Public Health Service, Centers for Disease Control and Prevention. NCEH Publication number 05-0570. Page 26 – S. Randall Humm NIOSH [1978]. Occupational exposure to inorganic lead. Cincinnati, OH: U.S. Department of Health, Education, and Welfare, Public Health Service Center for Disease Control and Prevention, National Institute for Occupational Safety and Health, DHEW (NIOSH) Publication No. 78-158. NIOSH [1984]. Current Intelligence Bulletin #42: Cadmium. Cincinnati, OH: U.S. Department of Health and Human Services, Public Health Service, Centers for Disease Control, National Institute for Occupational Safety and Health, DHHS (NIOSH)/DOL (OSHA) Publication No.84116. NIOSH [2005]. NIOSH pocket guide to chemical hazards. Cincinnati, OH: U.S. Department of Health and Human Services, Centers for Disease Control and Prevention, National Institute for Occupational Safety and Health, DHHS (NIOSH) Publication No. 2005-149. [http://www.cdc.gov/niosh/npg/]. Date accessed: March 2008. Thun JM, Elinder C, Friberg L [1991]. Scientific basis for an occupational standard for cadmium. American Journal of Industrial Medicine 20:629–642. 62 Fed. Reg. 206 [1997]. National Institute for Occupational Safety and Health; occupational exposure to inorganic lead: request for comments and information. Page 27 – S. Randall Humm bcc: B. Bernard (electronic copy) N. Burton (electronic copy E. Page (electronic copy) D. Sylvain (electronic copy) J. Riley (electronic copy) HETAB file room, HETA 2008-0055 (paper copy)